Tips for polishing stainless steel surfaces
Stainless steel - background to a versatile material
Stainless steel generally refers to alloyed steel grades that are usually corrosion and acid resistant and have a special degree of purity. Stainless corrosion-resistant steels are characterised by a minimum chromium content of 10.5%. The higher the proportion of chromium, the better the corrosion protection.
The four basic stainless steel grades
- Austenitic stainless steels (also known as CrNi steels) mainly contain chromium, nickel and molybdenum, with the nickel content usually being above 8% (rather soft, malleable, easy to weld, corrosion resistant, most commonly used in general purpose applications)
- Austenitic-ferritic stainless steels (duplex) consist of chromium, nickel and molybdenum with a Ni content of less than 8% (high strength, good weldability, highest corrosion resistance, enables particularly thin-walled constructions)
- Martensitic stainless steels mainly contain chromium as well as carbon or nickel (very hard and strong, used in tools, ball bearings, knives, etc.)
- Ferritic stainless steels ("chrome steel") are nickel-free and magnetic, easy to mould and machine (household goods, gas flue systems, etc.)
What does V2A or V4A stand for?
More than 100 years ago, Friedrich Krupp AG patented new types of steel based on the groundbreaking research of B. Strauß and E. Maurer. For the first time, these steels demonstrated optimal corrosion resistance coupled with good mechanical properties. The chosen abbreviations V2A/V4A stood for „Versuchsschmelze 2 / 4 Austenit“ (“Test Melt 2 or 4 Austenite”) and were extremely successfully marketed by ThyssenKrupp under the “Nirosta” brand for almost 100 years since 1922.
To this day, CrNi steels primarily used in metal construction with the material numbers 1.4301, 1.4541 and 1.4307 are still traded under the name V2A, and the CrNiMo steels primarily used in plant engineering with the material numbers 1.4401, 1.4571 and 1.4404 are traded under the name V4A.
Stainless steel applications
Stainless steel is frequently used in various industries, including construction and the food industry. Due to its high resistance to corrosion and acids, it is particularly suitable for applications where hygiene plays an important role.
The special degree of purity of stainless steel enables it to retain its properties even under extreme conditions. As a result, it can withstand both high temperatures and extreme cold without any problems. This makes it a versatile material. Another advantage of stainless steel is its durability. Thanks to the alloyed steel grades, the material remains resistant and robust over long periods of time. This means less maintenance and lower costs for repairs or replacements.
Stainless steel also offers aesthetic benefits: its shiny surface gives every product a modern look and is easy to clean - ideal for use in kitchens or other areas with high demands on cleanliness. Overall, stainless steel is a high-quality material with numerous positive properties such as durability, resistance to corrosion and easy care and cleaning options.
Thanks to these characteristics, stainless steel is widely used in a variety of sectors - from mechanical engineering to architecture - making it an indispensable component of modern industry.
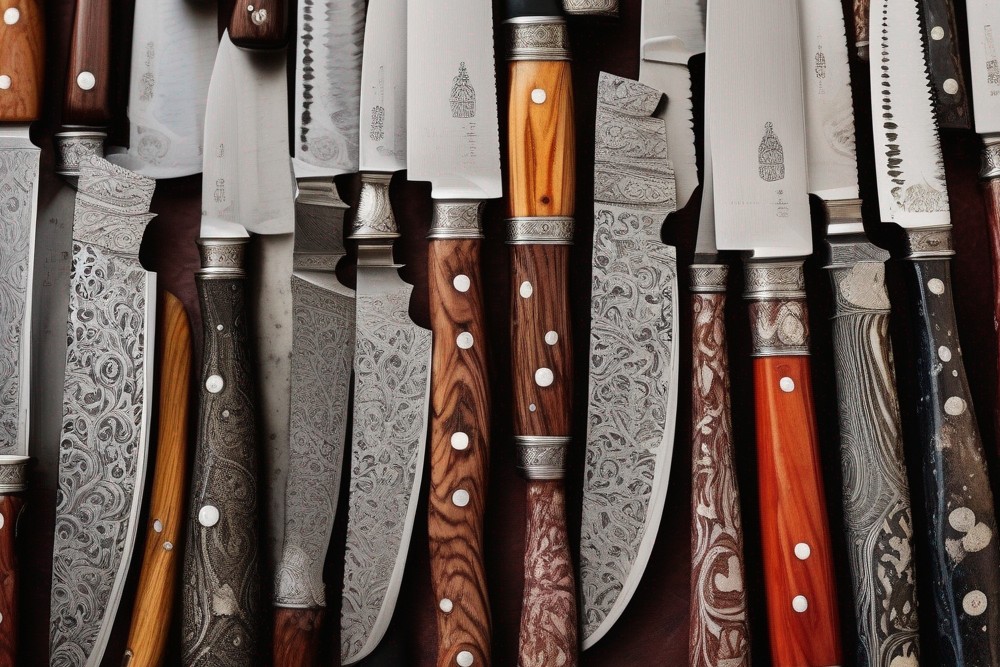
Basics of grinding stainless steel
A fine and particularly uniform finish is the prerequisite for an optimum polishing result on stainless steel. It is particularly important to achieve a high surface quality with the smoothest possible grinding pattern for the austenitic stainless steel grades with a low chromium content that are most frequently processed. This is because experience has shown that once defects have appeared on the stainless steel surface during grinding, the subsequent polishing steps can no longer compensate for them. Step-by-step grinding must then be repeated from the start.
Grinding in steps of decreasing grain size
Ideally, stainless steel is ground in a sequence of abrasives of increasing fineness. When selecting the abrasive, the rule of thumb is that the maximum grain size is halved in each step: e.g. P60 - P120 - P240 - P320.
The first sanding step usually starts with a very coarse grit (P35 - P60) to remove weld seams and rough imperfections first. In the case of cold-rolled steel, on the other hand, preliminary sanding tends to start with grit P60 - 120, followed by fine sanding with grits P120 - P240. Finally, the perfectly flat and flawless sanded surface is treated with grits from P320 - P400.
Practical tips for sanding
- As grain sizes decrease, the speed should also be reduced
- During fine sanding, do not apply too much pressure to avoid discoloration or coarse scratches.
- Austenitic stainless steel in particular dissipates the energy introduced much more slowly than the ferritic, chromium-alloyed types. The professional processing of austenitic steels therefore requires some experience, as for a perfect result the critical parameters such as contact pressure and speed, as well as the optimal sequence of grinding and polishing tools, must be precisely coordinated
- The individual grinding and polishing processes should always be carried out in cross grinding, i.e. as perpendicular as possible to the previous work step
- The working angle between the workpiece and the grinding wheel should be between 10 and 15 degrees
- The workpieces should be cleaned thoroughly after each grinding step in order not to carry over the coarser abrasives into the finer grinding
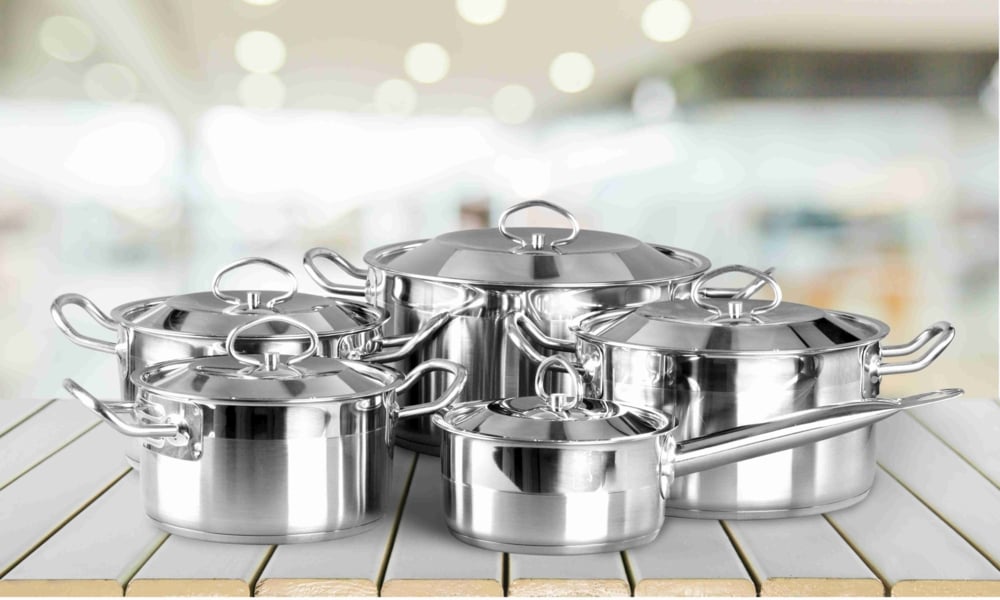
The basics of polishing stainless steel
For polishing stainless steel to a shine, we recommend a cutting speed of 30 to 35 m/s. It is important to limit the working temperature when polishing to around 50 to 60°C in order to avoid unwanted surface changes and tarnishing. This damage often cannot be reversed by further polishing. In addition, at higher temperatures there is a risk that thin sheets will warp. In order to control unfavorable temperature development, one should select the construction of the discs, limit contact times and control the immersion depth in the polishing disc.
Step-by-step polishing
The most important prerequisite for a fine mirror finish on stainless steel surfaces is to carry out several coordinated polishing steps. The decisive factor here is to refine the polishing pastes together with the discs in successive steps. From step to step, the step size between the grit sizes should be a maximum of 100 % (e.g. from grit 300 to grit 600 or from grit 600 to grit 1200 etc.). Polishing discs made of sisal or sisal nettle are particularly suitable for pre-polishing. Then switch to polishing discs made of firm cotton fabric for the main polishing. By polishing with polishing discs made of the finest molleton in seamless processing and a super finish polishing paste, you can finally achieve the finest shine on stainless steel, as is desired in yacht building, for example. For reworking and polishing hard-to-reach areas, we recommend our wide selection of polishing discs for drills.
Polishing sets to get you started
For a quick start, we offer you polishing sets for stainless steel that are tailored precisely to your project goals. With the help of our practical configurator, you can name your project goal and the available drive (e.g. drills, angle polishers or stationary polishing stands) and will then be taken directly to our product recommendations. Our polishing sets have been tested many times in terms of application technology and are constantly in use by our professional customers. EICKELIT polishing sets only contain high-quality polishing discs from our own production as well as precisely tailored professional polishing pastes.
Practical example of polishing to a super finish to yacht standard
Preliminary remarks
- Align polishing discs before use using a suitable dressing tool
- Wet the polishing discs sufficiently with the respective polishing paste at working speed.
- Adjust the contact pressure carefully! Too high a contact pressure and/or too low a speed can cause the workpiece to overheat, which often leads to an uneven surface (“orange peel”). This cannot be improved by further polishing and requires a new grinding process!
- Pay attention to cleanliness in the workplace. Contamination of polishing discs with abrasion from coarser polishing pastes must be avoided. The surface should always be carefully cleaned of any coarse paste residue before the subsequent, finer polishing step
- Our practical tip: after each use, store your polishing discs immediately in a dust-tight foil packaging
Step 1 - Pre-polishing
- First polish the carefully ground and cleaned surface to P320 - P400 in cross passes with a Sisal nettle pre-polishing disc type SB-VR together with the universal pre-polishing paste Menzerna 439T in quick moves at a cutting speed of approx. 25-30 m/s. After pre-polishing, the workpiece should have an even, satin-matt surface without scratches or grooves
- After pre-polishing, clean the surface thoroughly with a soft, lint-free cloth. If necessary, you can clean and degrease the surface with a suitable solvent or Viennese lime.
Step 2 - Main polish
- The evenly pre-polished and cleaned surface is now polished in cross passes with a polishing disc made of full-round blades N2550 and the medium-cut main polishing paste Menzerna P14F at a cutting speed of approx. 25-30 m/s until a beautiful shine is achieved
- After polishing, you should clean the surface again with a fresh, soft, lint-free cloth. Here too, you can degrease and clean the surface with a suitable solvent or Viennese lime
Step 3 - High-gloss polish
- The clean, brightly polished surface is now quickly polished to a flawless high gloss using a polishing disc made of N2501 full-round sheets and Menzerna P126 stainless steel high-gloss polishing compound at approx. 25-30 m/s in cross passes
- Please clean the surface again with a fresh, soft and lint-free cloth, if necessary together with a suitable solvent or Vienna Lime
Step 4 - Super Finish
- Finally, the very clean and high-gloss polished surface is quickly polished to a super finish using the seamless Effekta FM230 super-finish polishing disc and Menzerna P175 super-finish polishing compound at approx. 25-30 m/s in cross passes
- As the Super Finish polishing paste P175 is very dry, it only leaves an invisible microfilm on the now flawless stainless steel surface. To preserve the scratch-free shine, it is best to avoid any further mechanical cleaning after the super finish