Polishing Aluminium Rims
The tuning scene appreciates the flawless mirror shine of polished light alloy rims because of their spectacular appearance together with noble show cars. For this purpose, sophisticatedly designed aluminium rims are usually polished manually with polishing wheels to a perfect mirror shine. In order to show off the highest gloss to its full advantage, these high-quality refined aluminium rims are then often mounted on luxurious vehicles without any further protective coatings.
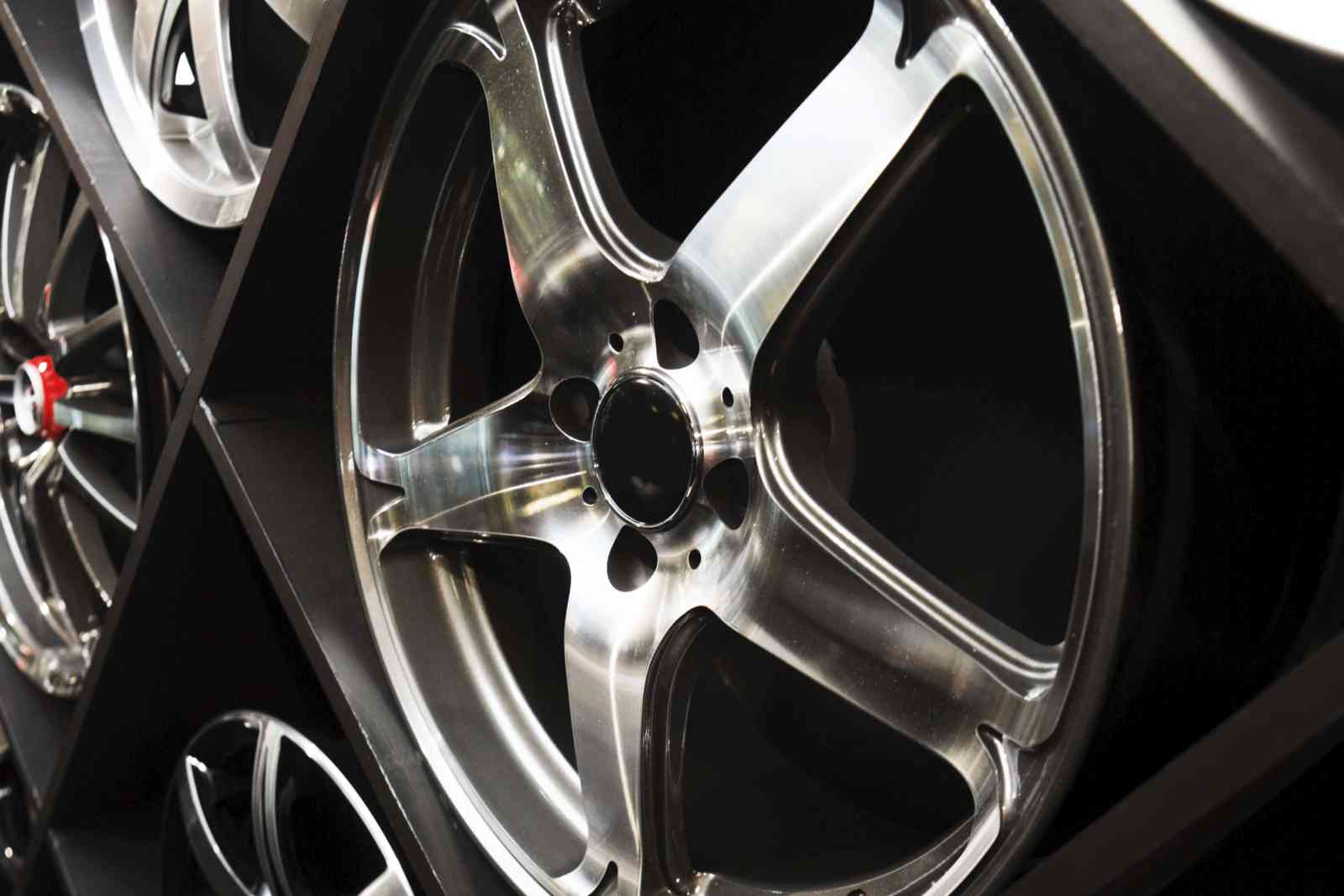
Beautiful Aluminium Rims - Critical Safety Components
In addition to this appealing look, the refined rims should also meet the highest technical requirements for the vehicles, which are usually powered at racing level. For unadulterated driving pleasure, refined aluminium rims in particular must therefore be designed for extreme loads. Consequently, the applicable technical and legal requirements must be strictly adhered to when embellishing and reconditioning vehicle rims. Otherwise, the approval of the aluminium rims for road traffic may expire in some countries or, in the worst case, serious accidents may occur.
In particular, only precisely defined and very small amounts of material may be removed at specified points (e.g. by grinding, blasting, etc.) during the machining of light alloy wheels. An aluminium rim must also not be thermally treated (e.g. paint stripping, baking, annealing etc.). This is because, according to the state of the art, aluminium can already lose its strength at the typical temperatures of paint stripping and baking. Thermally treated rims may therefore usually no longer meet the safety requirements originally specified by the manufacturer for road approval. In consequence, many European countries have adopted regulations that could lead to the expiry of such treated wheels' approval for road traffic.
Unrivalled high gloss through manual polishing
With the classic polishing of light alloy rims using manual processes with the help of sisal pre-polishing and cut-burring discs and cotton high-gloss finish buffing discs, a quality of mirror finish can be achieved, especially on forged aluminium rims, that could not be achieved by comparison with any alternative process. This is why manual polishing is still preferred in the tuning scene when it comes to a brilliant polishing result for the highest demands.
Since hand polishing removes very little material from the surface compared to other processes, an embellishment of high-gloss alloy wheels by manual, mechanical polishing can be repeated very often within the legal requirements without significantly affecting the safety-relevant mechanical properties of the wheels.
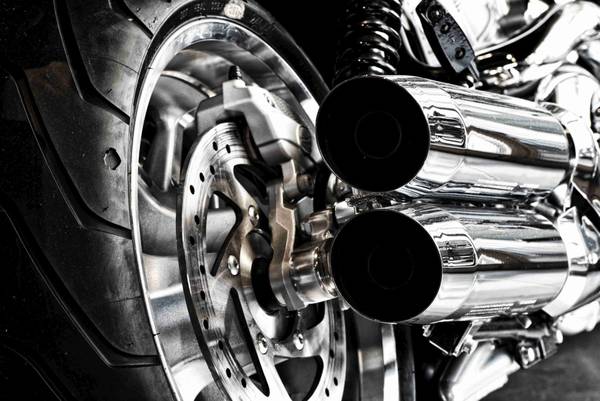
"High-gloss Compaction" - the better alternative?
Increasingly, aluminium rims are being offered on the market to be polished to a gloss finish with the help of vibratory finishing machines. These processes are often sold under the heading of "High Gloss Compaction or Densification" as the supposedly better alternative compared to conventional, manual polishing. Unfortunately, however, it is all too often underestimated that aluminium wheels prepared in this way have significant disadvantages and challenges compared to rims finished by hand polishing, in addition to some advantages:
Cost
Due to the high level of mechanical effort involved, mirror finishing is a very expensive process compared to hand polishing.
Elimination of Paint
High-gloss compacting of light-alloy rims requires that the rim has been completely freed from old layers of paint beforehand. The paint is removed mechanically, for example, by sanding or blasting with abrasive powders. Alternatively, paint layers can also be removed by chemical-physical treatment. Problems can arise if important prerequisites are disregarded:
- Excessive abrasion by blasting must be avoided, as otherwise the pores of the deeper material layers of cast rims could be exposed. This would prevent subsequent compaction or polishing and could also damage the load-bearing structure of the rim.
- Chemical paint stripping is often carried out at very high temperatures of up to 250° C, especially when removing powder coatings. Depending on the quality of the aluminium rim, this can lead to material weakening and consequently to its destruction
Limited Number of Repeated Treatments
Previously untreated cast rims can be processed well with the help of vibratory finishing machines due to their uniform and controllable removal. However, this is repeatable for only 1-3 reconditionings, because the vibratory finishing subsequently exposes deeper-lying, porous layers of the cast aluminium. Such rims can then no longer be polished to a high gloss and are usually no longer suitable for road use.
Durability
The very special, optical mirror finish effect of highly polished aluminium rims is most beautiful when the metal surface is free and unprotected. Unfortunately, however, the hope for long durability fuelled by terms such as "high-gloss densification" and "chrome look" often leads to disappointment, because even high-gloss densified rims are unfortunately very sensitive due to the unavoidable chemical and mechanical properties of aluminium and therefore only have a limited lifetime:
- Scratching due to mechanical influences such as cleaning and stone chipping
- Chemical attack by environmental influences or salt and thus increasing loss of high gloss
- Water stains when drying water containing mineral salts
Varnishes
To protect the elaborately created and sensitive high-gloss surface, attempts are often made to protect the exposed metal from environmental influences by applying a clear coat.
- Unfortunately, painted rims lose much of their brilliance compared to open metal surfaces.
- Generally, lacquers adhere only weakly to high-gloss aluminium surfaces. Therefore, even minor damage can lead to infiltration of the paint layer and consequently to rapidly progressing corrosion. A repair of such painted aluminium rims then usually requires a complete refurbishment of the entire rim.
- Due to the weak adhesion of the lacquer to an aluminium surface polished to a mirror finish, the entire workpiece is often enclosed in lacquer for effective protection of the metal. The closed polymer film is supposed to make the rim more durable because it prevents the paint from flaking off at the attachment points and avoids points of attack for infiltration with corrosive liquids. However, from a regulatory viewpoint it is problematic that overpainting the rim bed, the wheel hub or the seats of the wheel nuts is generally not permitted.
- Resistant, easy-to-apply and visually appealing powder coatings are often recommended for long-term protection of the high gloss rims that cost a lot of money. However, these paint systems require being baked at very high temperatures of up to 220° C for longer periods of time. At these temperatures, however, the modifications of the material structure characteristic of aluminium alloys already set in, which then frequently leads to a weakening of the mechanical stability and ultimately to the loss of approval of a rim treated in this way (technical background for further reading: Precipitation hardening).
Conclusion for manual rim polishing: Higher safety, more economy, better appearance
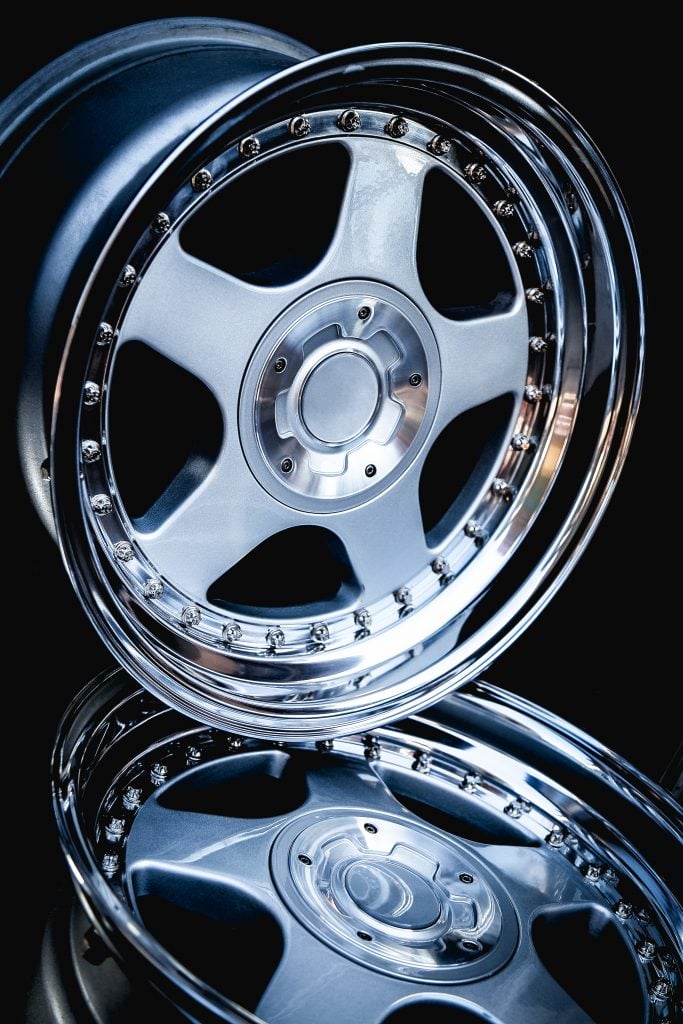
In summary, we recommend a rather conservative approach to our customers for the refinement of light alloy wheels. We believe this is the only way to combine a long-term visually appealing effect with a lot of driving pleasure and maximum safety.
For a noble mirror shine on safety-relevant vehicle components made of light metals, such as rims, we therefore recommend to our customers:
- Avoid high-temperature processes for chemical paint stripping of load-bearing components on aluminium wheels
- Ensure that there is no excessive mechanical removal by grinding or blasting
- Avoid any excessive thermal stress on light alloy rims for long periods of time
- Only polish your rims with suitable polishing wheels using the tools and procedures recommended by us.
- For light alloy rims, instead of using baked enamels (such as powder coatings, etc.), use alternative paint systems that cure at low temperatures.