Flap-Wheel | Non-Woven AO-007 | Customizable
AlOx / "Very Fine" / Grit 320
Ø 150 mm - 400 mm
Thickness: 30 – 60 mm
Abrasive Non-Woven Flap Wheels
EICKELIT flap wheels are constructed from a large number of single flaps of a nylon nonwoven with firmly bonded abrasives. They are suitable for cleaning, fine grinding, satin and matt finishing of non-ferrous metals and steels as well as a wide variety of other fields of application. We offer a large standard range of abrasive fleece types based on aluminum oxide or silicon carbide with different strengths and grain sizes to optimize desired results according to our customers' individual specifications.
Product Features
- Selectable grit sizes from "Extra Coarse" to "Ultra Fine" (grit 45 - grit 600 [CAMI])
- Core made of cardboard or hard paper tube, encapsulated with thermosetting synthetic resin compound
- Diameters 150 - 400 mm (larger diameters on request)
- Widths from 30 - 60 mm (wider rollers on request)
- Bore Holes 10 - 60 mm (hollow cores in standard industrial dimensions on request)
- Configurable in 4 ascending degrees of strength:
-
- H0: Low density, soft, flexible and adaptable, for easy processing of profiled workpieces with complex surface geometry
- H3: Medium density, high flexibility and adaptability, with increased resistance to clogging
- H5: High density, higher hardness and lower flexibility, resulting in increased service life and aggressiveness
- H7: Very high density, extreme hardness for high loads and strong aggressiveness
Abrasive Nonwovens
- In the manufacture of abrasive nonwovens, abrasives such as silicon carbide or aluminum oxide are firmly bonded to a nylon nonwoven by synthetic resins. Consequently, the strength and cooling effect of the abrasive fleece depends largely on the fiber strength, the fleece density and the physico-chemical properties of the binders in use
- Due to its open structure, abrasive nonwovens are self-cleaning and therefore do not clog during polishing. In addition, the chemical and physical resistance of the synthetic fiber composite also allows wet use together with aqueous or oily media
- Due to the flexibility of the nonwoen, even complex profiles and geometries can be efficiently processed, providing gentle material removal
- Because of the constant wear and tear of the backing material, fresh abrasives are constantly released in uniform concentrations on the tool's surface. This is why polishing tools made of nonwovens are particularly low-maintenance and thus provide a very uniform finish over their entire service life
- Please follow the link for further information on our range of available abrasive fleece variants
Corundum / Aluminum Oxide (AO)
Corundum consists of> 95% aluminum oxide and is the most frequently used grinding tool on bonded abrasives. However, as the degree of purity increases, the hardness and brittleness of corundum increase, which has a rather negative effect on the longevity of the abrasive grain and thus the uniformity of the grinding pattern. That is why we mainly use abrasive fleeces with doped and consequently more ductile types of corundum. On the one hand, this increases the service life of the polishing tools and, on the other hand, the grinding pattern looks more balanced compared to undoped aluminum oxide.
AO-007
- The aluminum oxide abrasive in AO-007 corresponds to a grain size of approx. Grit 240 and provides a very fine finish
- The abrasive fleece AO-007 has a medium-strength texture
Dimensions
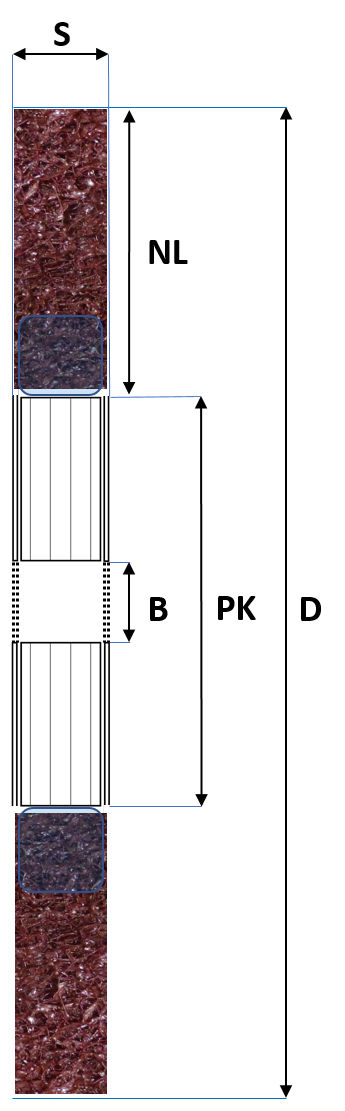
- * Observe safety regulations for the minimum diameter of drive shafts!
Bore Holes
- We manufacture your desired bore individually for you. We cover every known bore diameter for industrial polishing machines *
- If you need other bore diameters or special adapters (e.g. for hexagonal shafts, with keyways, etc.), we will be happy to manufacture them on request **
* Polishing discs drilled individually at the customer's request are excluded from exchange or return in accordance with our Terms of Cancellation.
** Observe safety regulations for the minimum diameter of drive shafts!
Thickness
- Non-woven flap discs can be freely configured with thicknesses of 30 - 60 mm *
- We are happy to manufacture non-woven lamellar rollers of other dimensions on request
* Tools manufactured individually at the customer's request are excluded from exchange or return in accordance with Section 7 Paragraph 1.1 “Non-prefabricated goods” of our terms and conditions.
Areas of Application
- Non-woven polishing tools are suitable for the surface treatment of metal (steel, INOX, non-ferrous metals and alloys) and non-metal surfaces (plastics, paints, wood, etc.)
- Their wide area of application includes for instance cleaning, descaling, deburring, fine grinding, roughening, matting, satin finishing, etc.
Application Instructions
- New abrasive fleece polishing tools must first be carefully run in until a uniform finish is achieved
- In order to avoid overheating and a subsequent disturbance of the surface structure that is difficult to correct afterwards, abrasive fleece polishing tools should be operated with as moderate to low pressure as possible
- Basically, the rule applies that a lower cutting speed produces a coarser matting image
- The following guide values apply to the typical cutting speeds of non-woven abrasive polishing tools:
- Non-ferrous metals 15-25 m/s
- Steels 15-25 m/s
- Thermosets 10-25 m/s
- Thermoplastics 8-15 m/s
- Acrylic glass 3-8 m/s
Protective Equipment when Polishing
When grinding and polishing, the work equipment used creates considerable health risks. It is therefore compulsory to wear suitable personal protective equipment for work safety when grinding and polishing. In particular, all rotating polishing and brushing tools may only be operated with suitable covers for reasons of occupational safety.
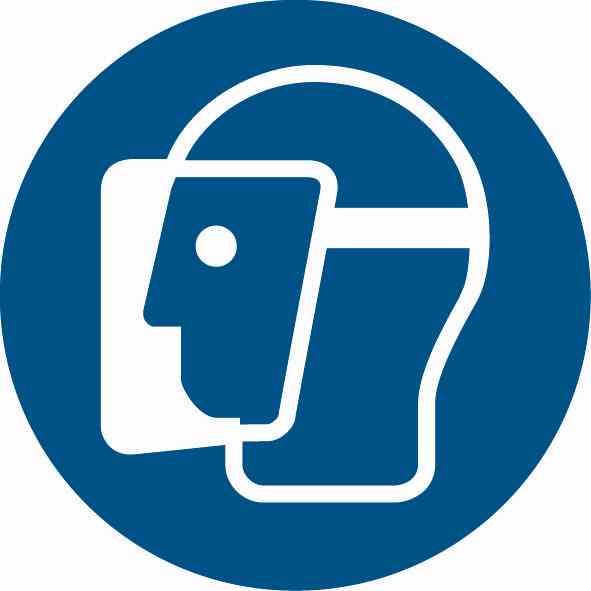
Wear eye / face protection
The fine dust emanating from polishing is harmful to the eyes. Flying parts can cause serious injuries to the face and eyes.
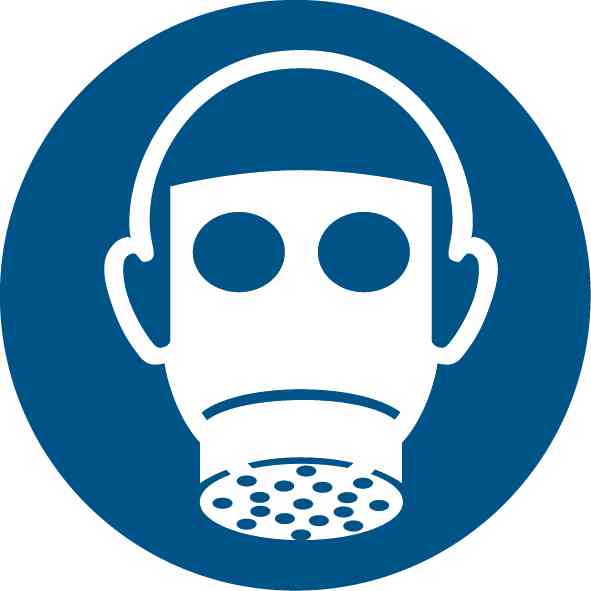
Wear respiratory protection
Fine dust contaminated with heavy metals and respirable, which can only be retained with suitable respiratory protection, is produced during polishing.
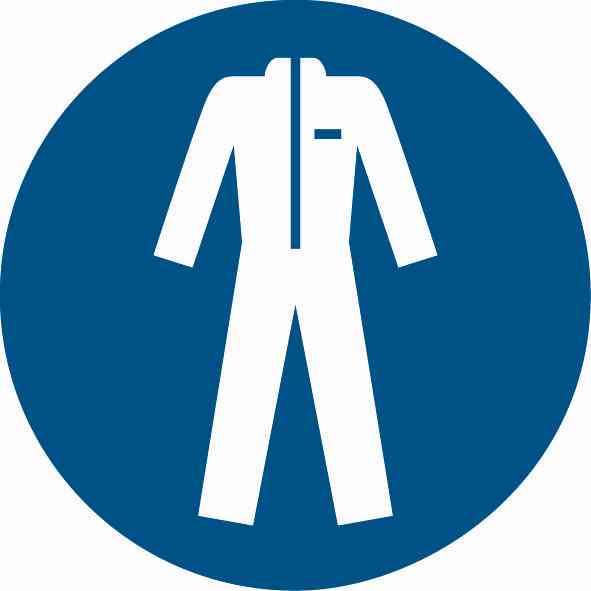
Wear protective clothing
Flying parts can cause sensitive injuries all over the body.
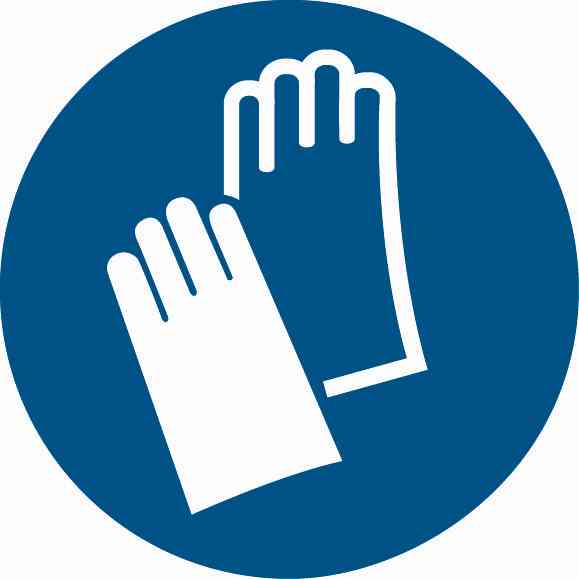
Wear gloves
In general, gloves should be worn when grinding and polishing. If there is a risk of being wound up (e.g. drills, processing small parts, etc.), gloves may be prohibited on the basis of a risk assessment.
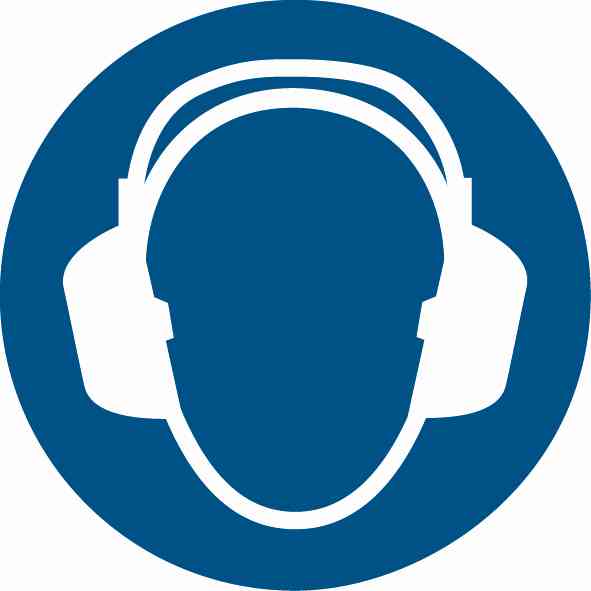
Wear ear protection
Due to the noise exposure during grinding and polishing, it is necessary to wear suitable hearing protection on a regular basis.
Details according to Regulation (EU) 2023/988 (GPSR)
Manufacturer
Menzerna polishing compounds GmbH & Co. KG, Industriestraße 25,76470 ÖTIGHEIM, info@menzerna.com
Responsible Person
Menzerna polishing compounds GmbH & Co. KG, Abteilung Produkt- und Umweltsicherheit, Industriestraße 25,76470 ÖTIGHEIM, sds@menzerna.com
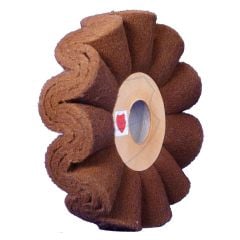
AlOx / "Very Fine" / Grit 320
Ø 200 mm - 400 mm
Thickness: 50 mm
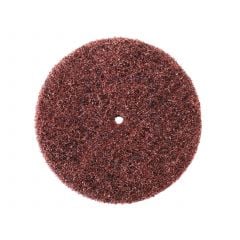
"Very Fine" AO-007 | Grit 320
Diameter 80 - 200 mm
Bore 12 mm
Packing Unit = 10 pc